- Gifts
- 1:4 Scale Engine Model
1:4 Scale Engine Model

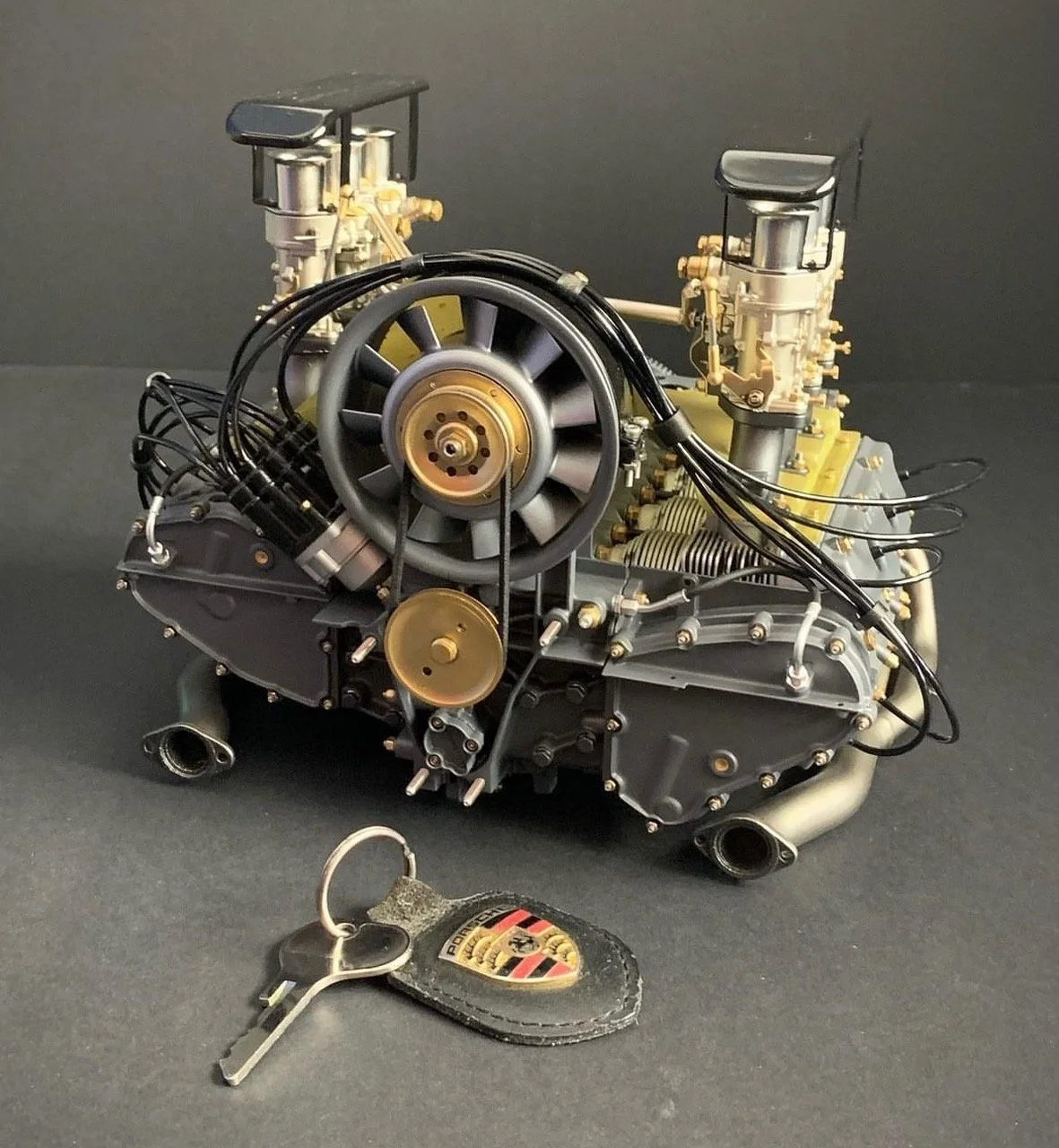


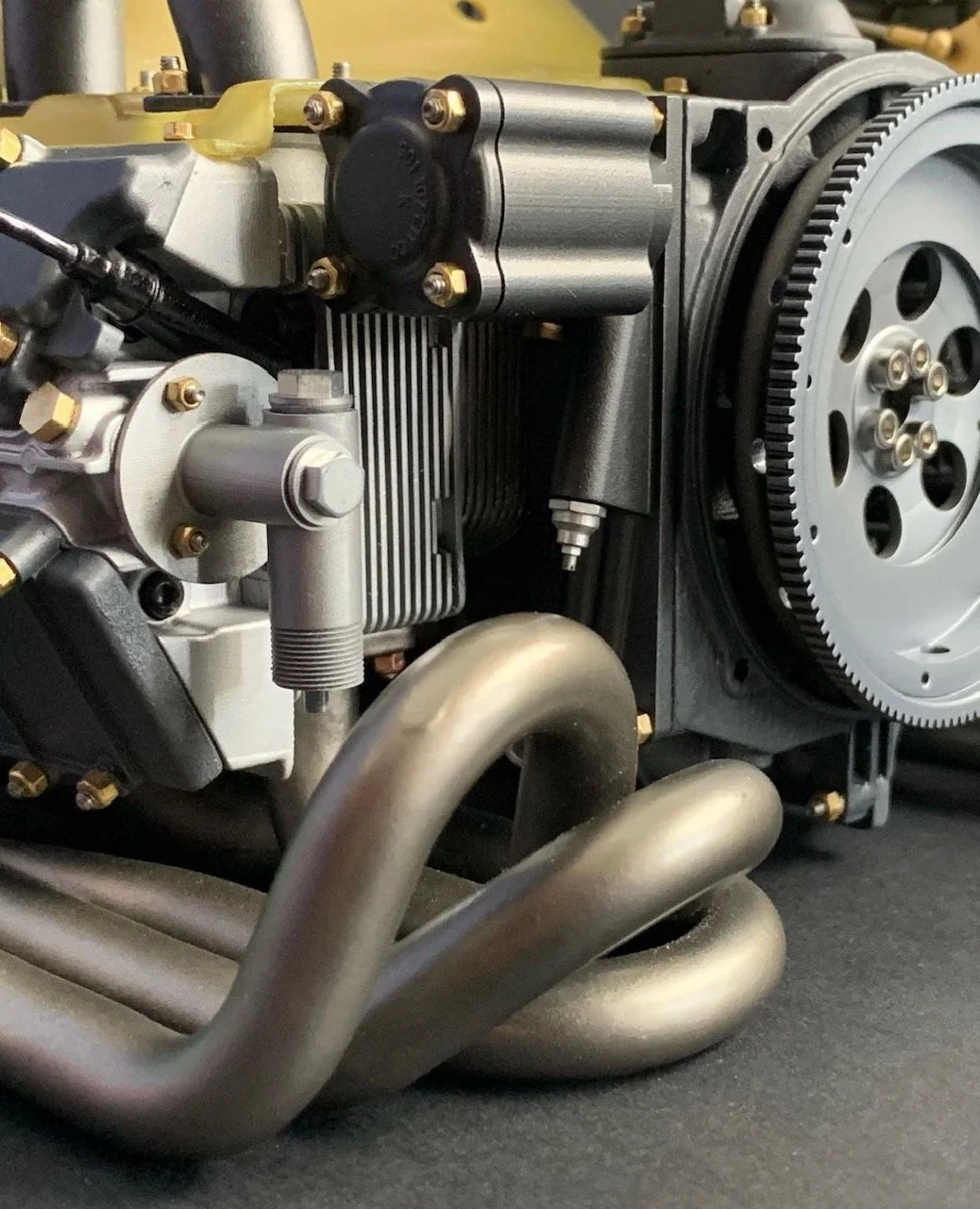



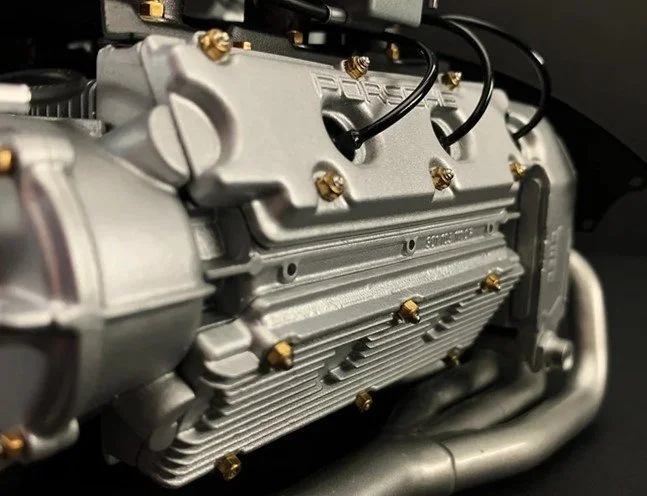

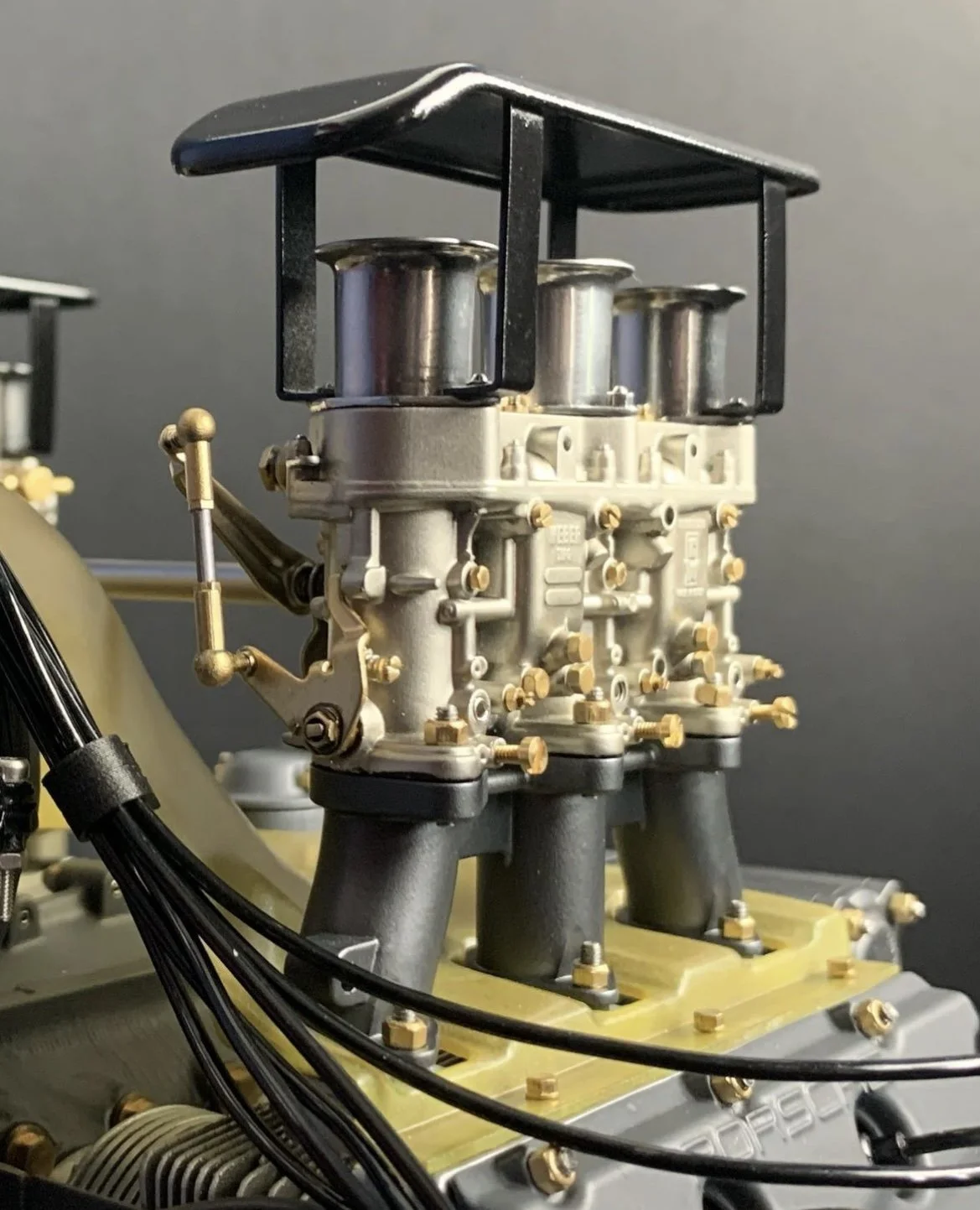
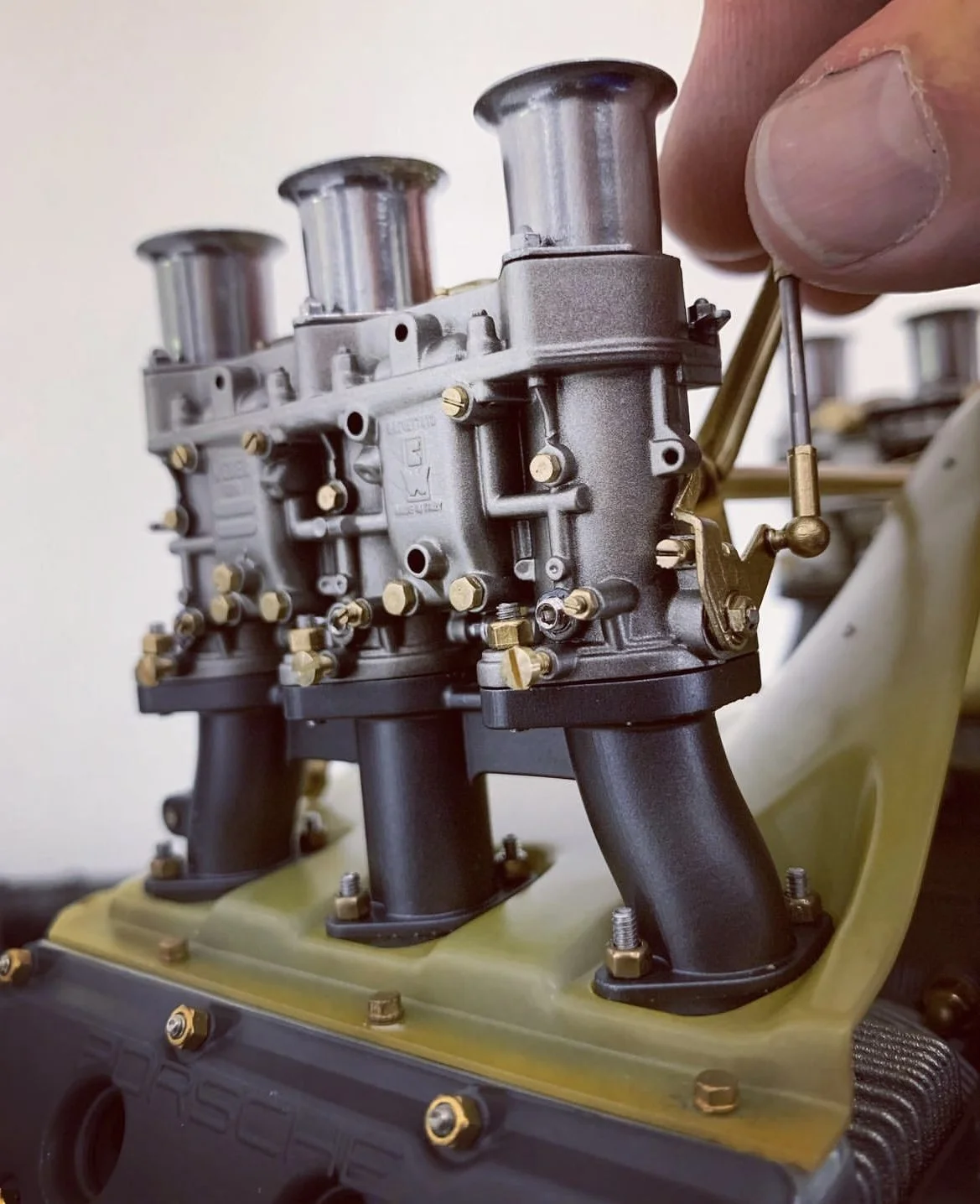

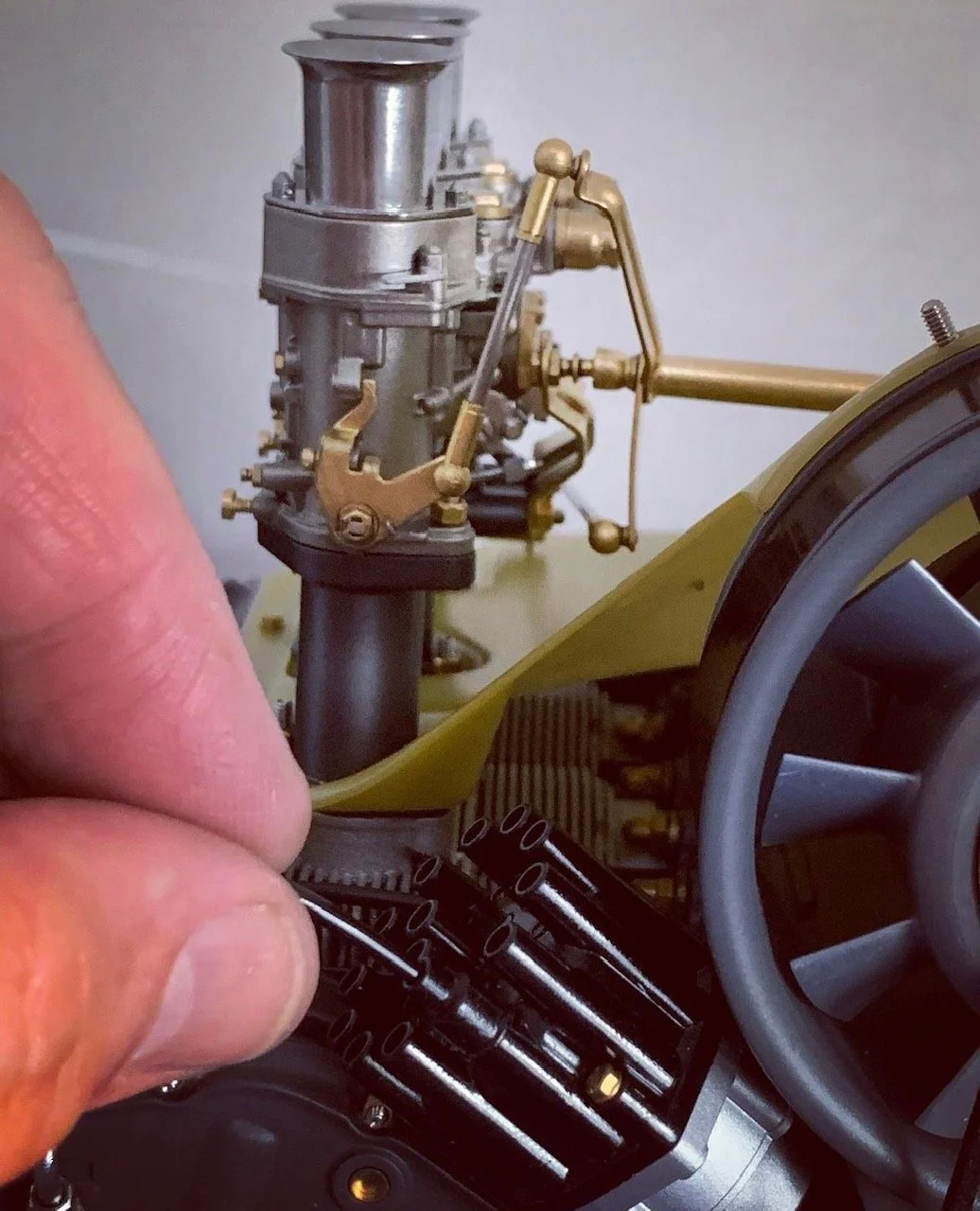
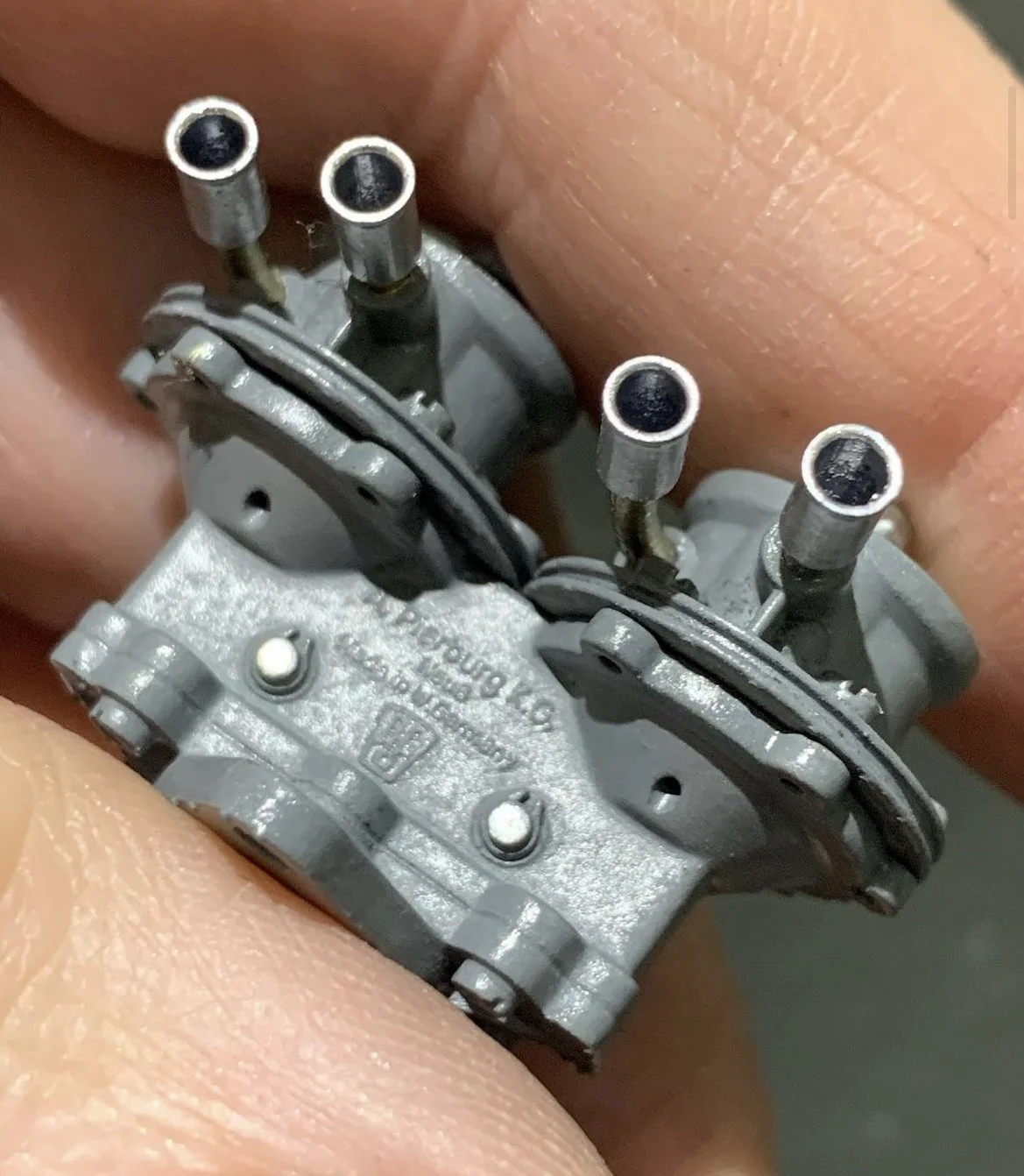
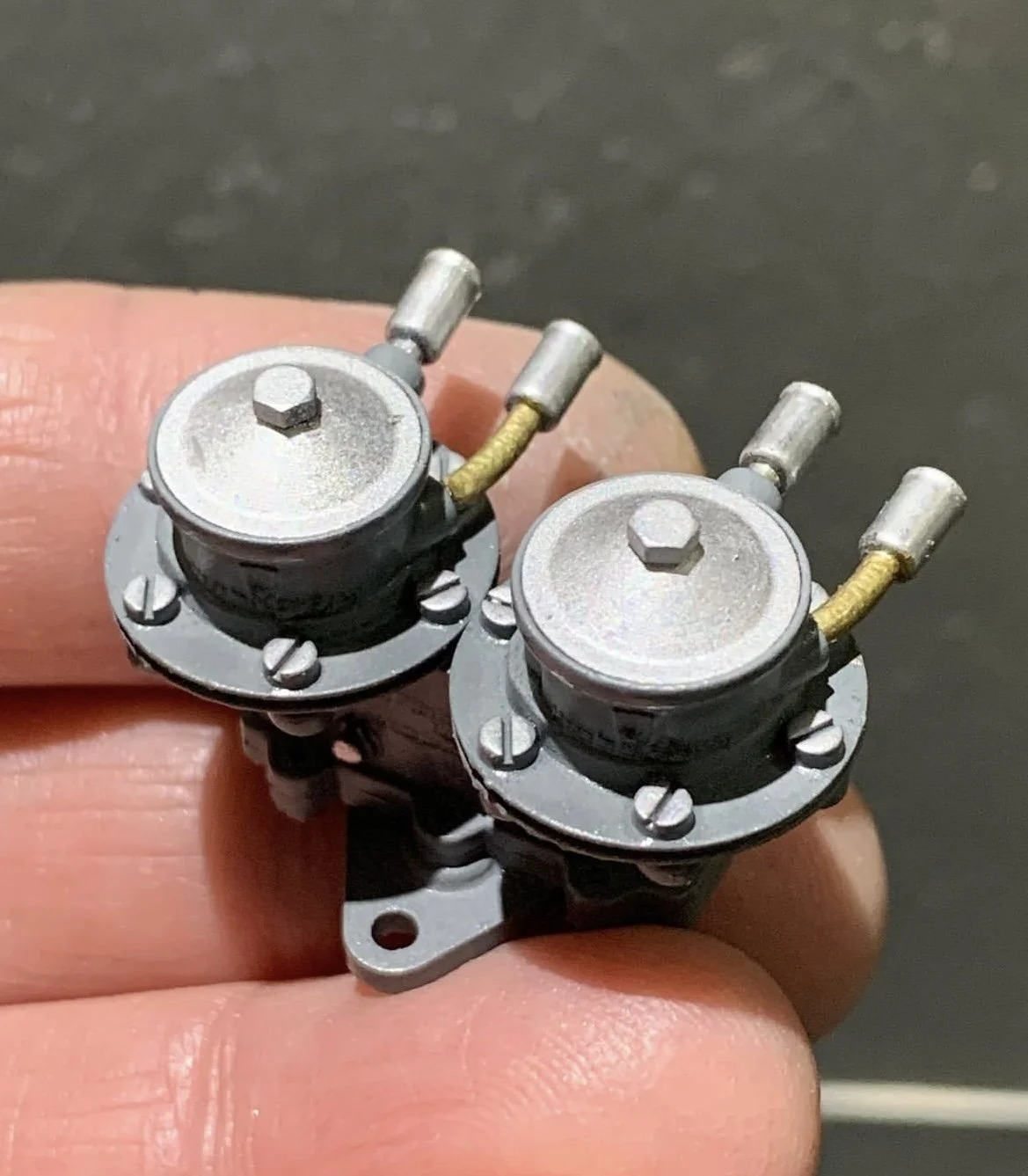
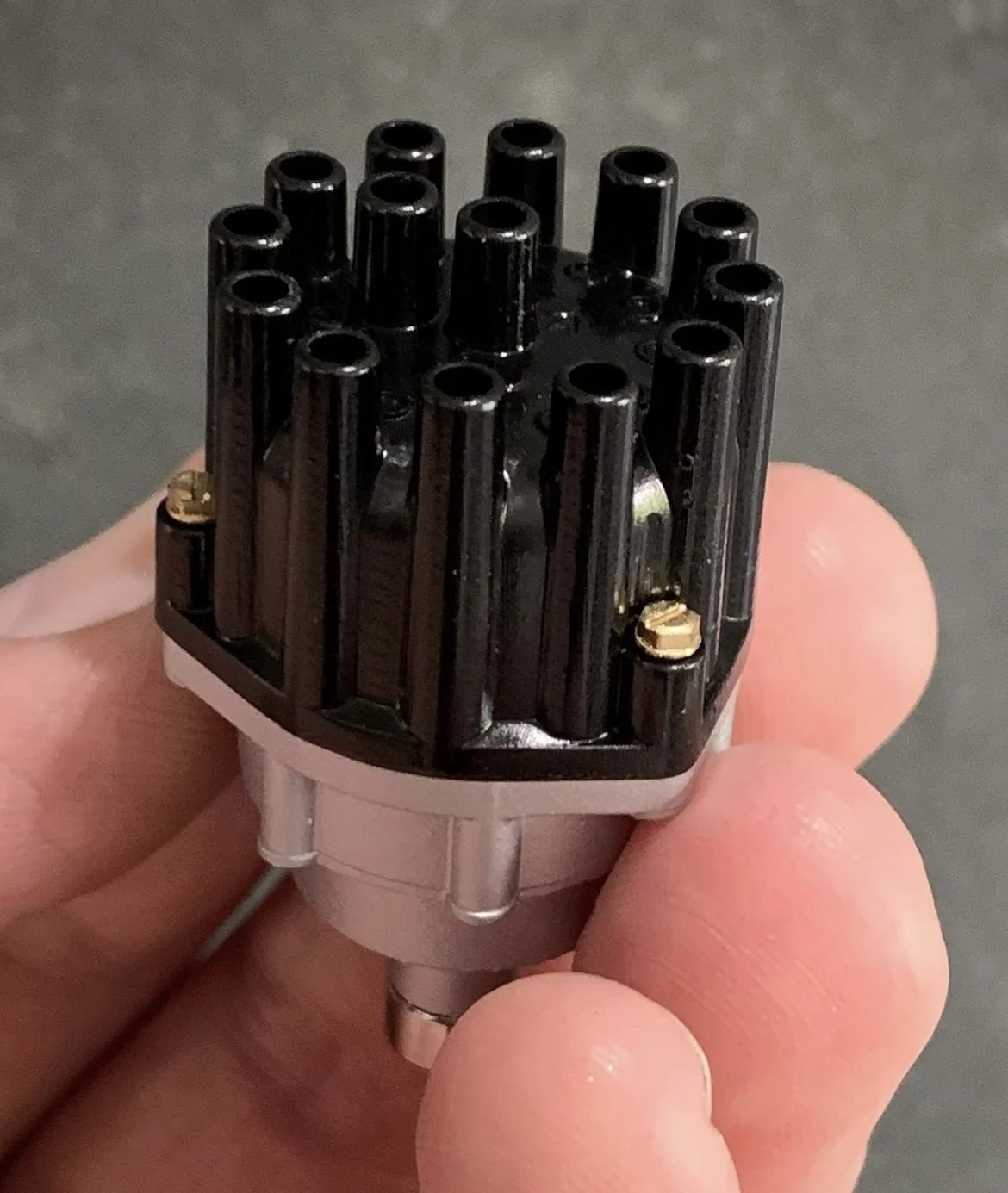




1:4 Scale Engine Model
Currently available in two versions:
901 2.0L Engine
911 R Engine
The Rationale
To those who rebuild air-cooled Porsche 911 engines it’s always a bittersweet moment when the engine is ready to go back into the car. On the one hand there’s the comfort of knowing that it will be good again for a few decades, on the other hand the sad reality that such a masterpiece will disappear into an engine bay where few will get to see it. This sparked a multi-year project to create a realistic 1:4 scale representation of the 911 engine, which is proportionally accurate in all respects, down to the smallest nut and bolt. Ducting, tinware and cabling (other than HT leads) are omitted to ensure an unobstructed view of the alloy castings which feature part numbers and stampings, even flashing and machining marks, as found on the original
The Project
To accurately produce such a complex model meant investing in the latest additive manufacturing technology. Every part had to be 3d-scanned in high detail, then digitised and in most cases completely redesigned to enable manufacturing on 1:4 scale without altering its outward appearance or proportions. This presented numerous challenges, for instance sourcing dimensionally accurate fasteners. Whereas M1.5 and M2 studs and nuts do exist (to represent the M6 and M8 fasteners on the full-scale engine), commercially available nuts are out of proportion when scaled back to full size. This type of compromise is acceptable in the scale model world but not on this project. Every nut on this engine is therefore 3d printed in resin and coated to represent zinc plating of the era.
All parts are perfect little replicas of the real thing and designed to fit together as tightly and accurately as possible. It starts with the engine block which is the heart of the engine and also the most complex component, both in terms of design and printing requirements. Even the smallest dimensional inaccuracy in this area means that something, perhaps much later during the build, won’t fit correctly. It’s therefore no surprise that the engine block took the longest to develop as part of what became a modular assembly system, which governs how all parts of this model fit together.
Great care was taken to replicate the textures and coatings used on the original engine as it left the factory, which meant hunting down and examining some extremely rare engines. Part numbers and manufacturer emblems are all faithfully replicated even on the smallest components. In many cases it’s only visible with a magnifying glass. It took over a thousand hours, spread over a period of 3 years, to arrive at the first prototype which proved that the idea was viable. It took thousands more hours before the model reached the current level of detail and finish.
Engine Details
The model is based on the original 1965 2.0 litre 911 engine (internal designation 901), the first iteration of the legendary flat six. One of the unique features of this rare engine (type 901/01) was the Pierburg mechanical fuel recirculation pump fitted to the chain housing with metal fuel lines running over the fan housing. The pump in this model consists of 12 individual parts which are all printed, post-processed and coated separately to mimic the various metals used in the assembly.
The carburettors in the model are printed in multiple pieces and feature jets, enrichment tubes and idling adjuster. Many of the details are barely visible without a magnifying glass, including the lettering on the carburettor body. Because of the intricate details and odd shape of the Solex carburettor, these turned out to be one of the most difficult parts to print. It took over 50 design and print iterations before the end result was acceptable. The metal plugs in the chain housings are printed and coated separately - a small but important detail to those who have restored these engines.
The sand cast texture is retained, on an almost microscopic scale, and the characteristic shimmer of aluminium es exactly as on the original. The scaled down M6 nuts require a magnifying glass to be truly appreciated.
Despite not having the internals of a real engine, turning the flywheel turns the pulley which turns the cooling fan. The fanbelt is custom made from polyurethane to accurately reflect the proportions of the original. The fan runs on roller bearings and the stainless-steel crankshaft is held by carbon fibre infused nylon bearings on either side. During assembly these bearings are lubricated with oil so it’s sometimes possible to detect traces of oil under the sump – not unlike the real thing!
Special tools are used during the preparation and assembly process. The exhaust headers for instance are held by custom designed clamps to enable unrestricted access from all angles while being airbrushed.
Unlike regular scale models, all parts are accurately scaled down and there are no compromises for the sake of easier manufacturing or assembly. This means that some components are so thin before being coated that that they are translucent. The fins inside the oil cooler for instance are less than 50 microns thick.
These are likely the most accurate 1:4 scale engine models ever produced, and are 100% made and assembled in the United Kingdom. We try to keep an engine in stock if you wish to view, but please get in touch beforehand. Please allow up to 12 weeks for an engine to be delivered from date of order. They are extremely labour intensive to assemble, and there is no fast way to speed up the assembly procedure of the hundreds of components.
It is possible to customise an engine with your own engine number if required, please get in touch for a quote. The engine is sold with a custom-made 3D printed box, that will safely secure your model engine during transport. You will want to take this and show your friends!
Free shipping on all items within North America!
Currently available in two versions:
901 2.0L Engine
911 R Engine
The Rationale
To those who rebuild air-cooled Porsche 911 engines it’s always a bittersweet moment when the engine is ready to go back into the car. On the one hand there’s the comfort of knowing that it will be good again for a few decades, on the other hand the sad reality that such a masterpiece will disappear into an engine bay where few will get to see it. This sparked a multi-year project to create a realistic 1:4 scale representation of the 911 engine, which is proportionally accurate in all respects, down to the smallest nut and bolt. Ducting, tinware and cabling (other than HT leads) are omitted to ensure an unobstructed view of the alloy castings which feature part numbers and stampings, even flashing and machining marks, as found on the original
The Project
To accurately produce such a complex model meant investing in the latest additive manufacturing technology. Every part had to be 3d-scanned in high detail, then digitised and in most cases completely redesigned to enable manufacturing on 1:4 scale without altering its outward appearance or proportions. This presented numerous challenges, for instance sourcing dimensionally accurate fasteners. Whereas M1.5 and M2 studs and nuts do exist (to represent the M6 and M8 fasteners on the full-scale engine), commercially available nuts are out of proportion when scaled back to full size. This type of compromise is acceptable in the scale model world but not on this project. Every nut on this engine is therefore 3d printed in resin and coated to represent zinc plating of the era.
All parts are perfect little replicas of the real thing and designed to fit together as tightly and accurately as possible. It starts with the engine block which is the heart of the engine and also the most complex component, both in terms of design and printing requirements. Even the smallest dimensional inaccuracy in this area means that something, perhaps much later during the build, won’t fit correctly. It’s therefore no surprise that the engine block took the longest to develop as part of what became a modular assembly system, which governs how all parts of this model fit together.
Great care was taken to replicate the textures and coatings used on the original engine as it left the factory, which meant hunting down and examining some extremely rare engines. Part numbers and manufacturer emblems are all faithfully replicated even on the smallest components. In many cases it’s only visible with a magnifying glass. It took over a thousand hours, spread over a period of 3 years, to arrive at the first prototype which proved that the idea was viable. It took thousands more hours before the model reached the current level of detail and finish.
Engine Details
The model is based on the original 1965 2.0 litre 911 engine (internal designation 901), the first iteration of the legendary flat six. One of the unique features of this rare engine (type 901/01) was the Pierburg mechanical fuel recirculation pump fitted to the chain housing with metal fuel lines running over the fan housing. The pump in this model consists of 12 individual parts which are all printed, post-processed and coated separately to mimic the various metals used in the assembly.
The carburettors in the model are printed in multiple pieces and feature jets, enrichment tubes and idling adjuster. Many of the details are barely visible without a magnifying glass, including the lettering on the carburettor body. Because of the intricate details and odd shape of the Solex carburettor, these turned out to be one of the most difficult parts to print. It took over 50 design and print iterations before the end result was acceptable. The metal plugs in the chain housings are printed and coated separately - a small but important detail to those who have restored these engines.
The sand cast texture is retained, on an almost microscopic scale, and the characteristic shimmer of aluminium es exactly as on the original. The scaled down M6 nuts require a magnifying glass to be truly appreciated.
Despite not having the internals of a real engine, turning the flywheel turns the pulley which turns the cooling fan. The fanbelt is custom made from polyurethane to accurately reflect the proportions of the original. The fan runs on roller bearings and the stainless-steel crankshaft is held by carbon fibre infused nylon bearings on either side. During assembly these bearings are lubricated with oil so it’s sometimes possible to detect traces of oil under the sump – not unlike the real thing!
Special tools are used during the preparation and assembly process. The exhaust headers for instance are held by custom designed clamps to enable unrestricted access from all angles while being airbrushed.
Unlike regular scale models, all parts are accurately scaled down and there are no compromises for the sake of easier manufacturing or assembly. This means that some components are so thin before being coated that that they are translucent. The fins inside the oil cooler for instance are less than 50 microns thick.
These are likely the most accurate 1:4 scale engine models ever produced, and are 100% made and assembled in the United Kingdom. We try to keep an engine in stock if you wish to view, but please get in touch beforehand. Please allow up to 12 weeks for an engine to be delivered from date of order. They are extremely labour intensive to assemble, and there is no fast way to speed up the assembly procedure of the hundreds of components.
It is possible to customise an engine with your own engine number if required, please get in touch for a quote. The engine is sold with a custom-made 3D printed box, that will safely secure your model engine during transport. You will want to take this and show your friends!
Free shipping on all items within North America!